|
The Shipbuilding market in 2004 (2) |
|
Analysis by country
|
Asia
|
|
South-Korea
2004 was a new record year for Korea, which once
again confirmed its role as world leader. The Korean
orderbook went from 49 to 62 million gt between the end
of 2003 and year-end 2004. By contrast the Korean
orderbook stood at only 27 million gt at the end of
2002.
All the yards are full until the first or second
quarter of 2008, with only very limited exceptions.
Within some yards, certain berths are committed up
until the end of 2008.
Korean shipbuilding remains very concentrated. The
Korean portfolio, which represents slightly over 1,100
ships, is split up between 15 shipyards.
The orderbook of the three largest Korean builders
Hyundai Heavy Industries (HHI), Daewoo Shipbuilding and
Machinery Engineering (DSME) and Samsung Heavy
Industries (SHI), are largely focused on the very large
containerships, LNG carriers and tankers (VLCCs,
Suezmax, Aframax). Hanjin exclusively builds very large
containerships.
Hyundai Mipo Dockyard and STX, who have previously
concentrated on product tankers, have now considerable
orders of containerships, of 2,800 teu for the former
and from 2,700 to 3,500 teu for the latter. Shin-A
remains concentrated on building Medium Range
product-chemical carriers.
The smaller Korean shipyards have been ambitious and
have succeeded in making a remarkable presence on the
international scene. INP has attracted the very top
names in the shipping industry and by year-end 2004
could count 20 ships on order. Others like 21st
Century, Samho, Nokbong, Kwangyang have succeeded in
selling extensive
series of product tankers of 5,500 dwt, 12,800
dwt, and 13,000 dwt to different owners. Daesun
continues to be active in the construction of
containerships of 900 to 1,100 teu.
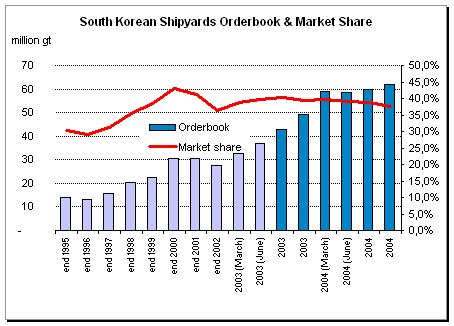
How have the Korean shipyards been able to increase
their portfolio from 49 million to 62 million gt
without creating a single new berth?
Above all, by spreading out over time their
orderbook, and by constantly improving their
productivity, but also by opening new docks.
HHI has used its dry-land building facility, usually
dedicated to offshore units, to build a series of 16
Aframaxes. STX has recovered its old construction site
in Busan (ex Daedong), now renamed STX-Busan, to build
a series of 12 product tankers of 10,000 dwt for
Clipper. DSME and SHI have invested heavily in floating
docks. Recourse to sub-contracting, especially for
steel blocks, has grown. SHI, which possesses a steel
blocks factory at Ningbo in China, intends to increase
its production from 60,000 to 200,000 tons as of 2005
(corresponding to the equivalent of 5 VLCCs or 8 LNG
carriers). Hyundai Corporation has decided to invest in
a Chinese shipyard, Lingshan, near to Qingdao.
The Sun Dong shipyard, which specialises in the
building of blocks, has decided to launch itself into
newbuildings and has signed contracts for a series of
Panamax bulkers which should become effective upon
receipt of bank refund guarantees.
Some Korean shipyards (DSME, STX) also have plans to
expand in China which remain to be materialised. Others
like HHI and HMD could give priority to new
developments in North Korea when the moment comes.
South-Korean shipyards are worried about having
filled their orderbooks too early and at too low
prices. By the end of 2004, it was obvious that several
Korean shipyards were facing difficulties in spite of
higher sale prices. |
Japan
2004 was also a new record year for Japan,
which confirmed its second place among world
leading shipbuilding nations.
Japanese builders' orderbooks went from 43 up
to 54 million gt between end 2003 and year-end
2004. It was 24 million gt at year-end 2002.
All the yards are generally full until 2008,
but certain are committed up to 2009. Contracts
for such late delivery dates might not be signed
before another year or two, but berths are already
booked.
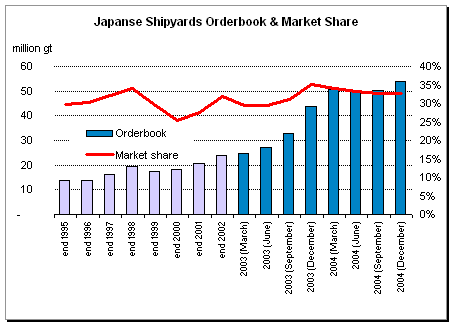
Even more than elsewhere, Japanese shipyards
give priority to their dynamic domestic owners and
it has become more and more difficult for a
foreign owner to place an order with them. It
seems that Japanese owners are also less demanding
and even more accommodating than their foreign
counterparts, this has had a visible impact on
the number of hours spent on each ship and on the
final net result of each building contract.
Japanese shipbuilding industry is less
concentrated than in South Korea. The Japanese
portfolio, which has practically an identical
number with more than 1,100 ships, is spread out
between fifty construction sites.
How have Japanese shipyards been able to
increase their portfolio from 43 million to 54
million gt?
Above all, this has been achieved through
extending their orderbook over a longer period of
time, up until 2009 for some yards. Additionally,
it has been achieved by a constant improvement of
their productivity. For instance, at the beginning
of February 2004, Mitsubishi announced that they
were planning to reduce the construction time of a
VLCC between keel-laying and delivery from 7 to
5.5 months.
New production capacity has also been created.
Imabari opened a new site specialising in the
construction of bulkers. Naikai Zosen has absorbed
its affiliate Nichizo IMC to improve
productivity. Murakami Hide has expanded one dock. Other yards, such as Namura and
Kyokuyo, have decided to invest in new workshops
and lifting equipment to increase the size of the
berths and the number of ships they can handle.
Proximity with China, where Japanese owners
like NYK and K Line have already placed orders,
could represent a danger for Japanese builders.
But it has also been an opportunity as they can
increase their purchases of equipment and
sub-contracting there. Tsuneishi has created a
production site for steel blocks in the province
of Zhejiang. The success of NACKS shipyard, opened
in 1998 in Nantong (China) -a joint venture
between the Japanese builder Kawasaki Heavy
Industries and the Chinese owner Cosco- is another
example of co-operation and possible development.
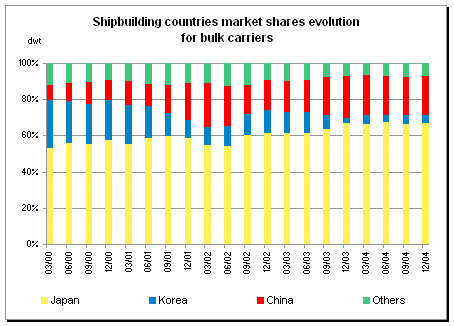
One has to admire the perseverance and dynamism
of Japanese shipyards. They reflect the ambition
of Japan, a developed country with a well-paid
workforce, not only to maintain but also to
develop shipbuilding in a highly industrialised
country. Japan demonstrates that it is possible to
build ships at market prices with a more expensive
workforce than in Korea and China, thanks to a
remarkably high level of organisation and highly
automated production process.
|
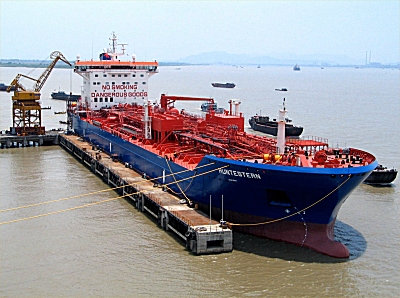
|
Huntestern
37,179 dwt, built in 2004 by Jinling, owned by
Rigel Schiffahrts
|
China
2004 was also once again a record year for China,
which confirms its third place in the world ranking.
The orderbook of Chinese builders went from 17 to
26 million gt between year-end 2003 and year-end 2004.
In 2002, by comparison, the Chinese orderbook stood at
9 million gt. It is a remarkable performance when we
remember that the orderbook of Japanese builders was 24
million gt at the end of 2002.
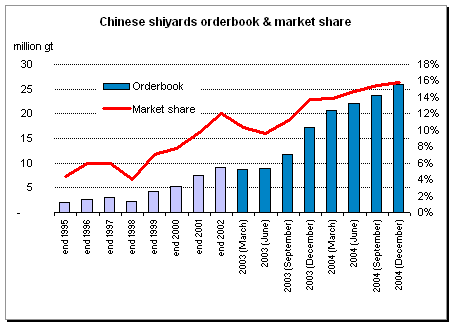
Contrary to their Japanese and Korean counterparts,
Chinese yards still have some berths available
in 2008.
The strength of the Chinese orderbook is not only
explained by having been spread out over 3 years but,
above all, by the expansion of existing facilities and
the creation of new shipyards. There are about two
hundred shipyards with merchant ship building capability in
China and about fifty competing on the international
market.
Signing of new building contracts in China generally
takes a longer time than in Korea and Japan. Whilst
this was a handicap to Chinese yards in the middle of
the Asian crisis in 1998, when prices were falling, it
was rather to their advantage in 2004 with a rising
market. They have been able to adjust their prices
closer to the market. One should also be aware of the
arrival of a new generation of management in the
shipyards, more internationally minded and much better
informed, thanks largely to the internet, who carry out
a close monitoring of the markets.
Nonetheless, this rapid development is not without
some hitches, and even some frustration with clients of
certain provincial shipyards. Letters of intent have in
some cases not been transformed into firm contracts at
agreed prices, signed contracts have not been
formalised, options have not been confirmed or at least
not on agreed terms, etc. Some yards have encountered
real problems in obtaining financial support from their
bankers who criticise them for having signed at too low
levels which are insufficient to cover their costs.
Some even had to renegotiate contracts with their
clients, facing rising costs and weak financial
situations.
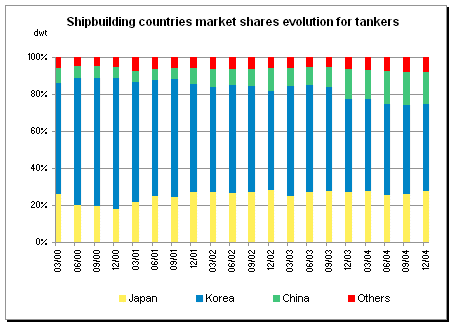
Chinese shipyards work in a constantly changing
environment and have to juggle with a number of
difficulties. They have been affected by energy
shortages and steel or main equipment
supplies, like engines, which they had to buy abroad at
higher prices.
Chinese shipyards should pursue their efforts to
produce quality ships. In the current market, they have
been able to benefit from the rise in prices and, above
all, to obtain terms and conditions on par with their
Korean and Japanese competitors. The expectations of
owners on the quality front are high, and it is
important not to deceive them as the reputation of
Chinese yards is at stake. Quality is the best way
to reduce costs. To deliver a good vessel, in order to
avoid expensive surveys, repairs, waste of materials or
even problems that can compromise ship's operations
once in service, is the best way to save money.
Expansion projects and creation of new shipyards are
continuing, but some ambitions have been contained. The
central government has put a hold on credit access and
some projects have not obtained the necessary
government authorisations. The ambitious project of
Nantong Rongshen seems to be one such casualty.
Restructuring is taking place. Shanghai Shipyard has
left the centre of Shanghai for the island of Chong
Ming. Chengxi and Shanghai Shipyard are now part of the
same group. Jiangdu shipyard has been taken over by the
private group Sinopacific, which now controls three
yards: Zhejiang, Dayang, and Dadong. Dalian (old) and
Dalian New have restructured their management.
As with the Japanese yards, Chinese shipyards have
also given priority to domestic owners who have
enormous needs.
Hudong Zhonghua has signed up this year for two LNG
carriers of 147,000 cbm for delivery in 2006 and 2007
in the context of the Guangdong project. Negotiations
are in process for two supplementary ships intended to the Fujian project. Chantiers de
l'Atlantique (France) are undertaking the technology
transfer.
The yuan vs dollar fixed parity offers an undeniable
competitive advantage to Chinese builders, even if they
have to purchase a large share of equipment in Europe,
Korea, or in Japan. There were talks between governments
this year about adjusting this parity, and even to
float the Chinese currency. The Chinese yards have even
sometimes used this possibility as a sales pitch.
Chinese shipyards are in an enviable position, since
most investments are the result, directly or
indirectly, of the government. Shipyards in other
countries, particularly in Europe, would be delighted
to be able to benefit from such a support to modernise
their production base, without bearing the costs.
China is investing in some gigantic shipbuilding
sites, capable of competing in the future with the
biggest Japanese or Korean facilities. There are
currently 8 docks for building a VLCC in China,
compared to 14 in Korea and 14 in Japan. By 2008 /
2009, China might have no less than 22 VLCC docks. One
can however fear that this expansion plan will come to
overturn the existing equilibrium and destabilise the
industry in the coming years. In a short while, Chinese
shipyards will be in direct competition with Japanese
and Korean shipbuilders for the same types of ships
(VLCC, LNG, very large containerships).
|
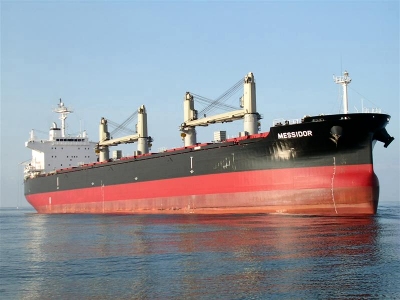
|
Messidor
55,300 dwt, built in 2004 by NACKS, owned by
Setaf-Saget (Groupe Bourbon)
|
Taiwan
The orderbook of Taiwanese builders went from 1.9 to
3.2 million gt between year-end 2003 and year-end 2004.
Taiwan thus occupies the 5th place in the world
ranking.
The state shipyard CSBC gave priority to domestic
owners such as Yang Ming, Wan Hai and China Steel
Corporation. Their orderbook extends until end 2008 and
comprises essentially containerships: with a capacity
of 1,800 teu in Keelung and of 4,250, 5,250 and 6,000
teu in Kaohsiung, as well as a few Capesize bulk
carriers of 200,000 tons.
Other countries in the Indo-Asian zone
The search for newbuilding sites has pushed owners
to less traditional destinations.
Ha Long and Nam Trieu shipyards of the Vinashin
group in Vietnam signed up with Craig from the UK, for
an important series of Handymax dry bulk carriers of
53,000 dwt. Danish owner Clipper placed an order for
several Handysize bulk carriers of 30,000 dwt with
Cochin shipyard in India.
Iranian shipyards have signed some noteworthy orders
with domestic accounts and are now looking for some
international clients. Dubai Drydocks has booked its
first order for bunkers vessels of
6,500 dwt. Others should follow.
|
Europe
|
|
The search for construction sites with early delivery
dates
has also brought owners towards European shipyards.
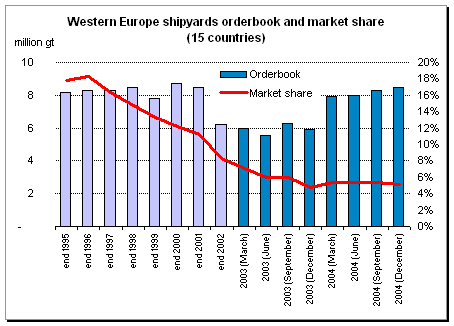
The European shipyards have benefited from the
overflow of a saturated Asia. They have been able to
offer earlier deliveries: 2006 as against 2007 or 2008,
for which owners have been prepared to pay a premium.
The mainstream of business for Asian shipyards being
standard ships, the recovery of demand for specialised
tonnage has certainly helped the European yards to regain
some ground.
It is worth stressing that the West European
orderbook has progressed this year for the first time
for ages. They have moves up from 5.9 to 8.4 million gt
between end 2003 and end 2004.
It is of course a pleasure to see this recovery of
business. But the basic handicaps of West European
shipyards in comparison with their Asian competitors
still remain: dispersed production, poor investment,
ageing installations and workforce, unfavourable tax
regimes, high social security costs, too much
bureaucracy and too few effective working hours.
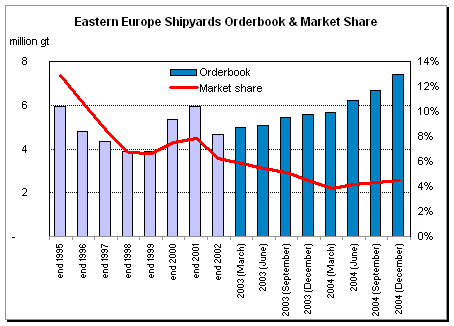
The drop of the dollar against the euro and the
impending termination of subsidies of up to 6 % on
March 31st 2005 will not help the European shipyards'
task.
It is a pity to see that there is not a more
efficient European industrial policy. Too much public
money is spent to reduce workforce, to put employees on
early retirement or to close yards. It should be
possible to conceive of a more proactive and wilful
policy aimed at using the inherent social funds to help
the industry to adapt, develop, and prepare for the
future rather than liquidate the past. Japan has
demonstrated that this option was not totally illusory.
|
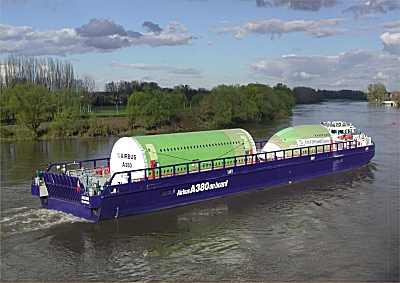
|
Breuil
600 dwt, self-propelled barge, delivered in 2004
by De Hoop, operated by Socatra, dedicated to the
carriage of blocks of the A380 airplane on the
Gironde estuary
|
France
The orderbook of French shipbuilders has gone from
380,000 gt at year-end 2003 to 450,000 gt year-end
2004.
Gaz de France decided to entrust the building of
another LNG carrier of 153,000 cbm to Chantiers de
l'Atlantique, which took their total backlog of such
ships to three. As with the two preceding ships, signed
in 2002 and 2003, this one will be equipped with a
diesel-gas-electric propulsion, the power being
provided by gas engines. It is also the method of
propulsion that AP Moller has adopted this year with
its orders at the Korean shipyard Samsung.
Chantiers de l'Atlantique have taken advantage of
the revival in the cruise market and signed up two new
ships of 90,000 gt and 3,000 passengers with
Mediterranean Shipping Cruises who, on their side, have
taken delivery of the 'MSC Opera', a passenger liner of
59,058 gt, with 795 cabins.
But Chantiers de l'Atlantique, faced with a
declining demand for cruiseships compared to the glory
years of the late 1990s, need to adjust their building
capacity, which should be reduced from 5.5 to 2.5
equivalent cruiseships. This reduction in capacity
should be accompanied by a reduction in the workforce,
a drive for further economies of scale with a more
important reliance being placed on sub-contracting and
Asian supplies.
The Piriou shipyards delivered two fishing vessels,
a tug boat and a PSV. They are building 5 trawlers, 3
tuna purse seiners - one of which is 83 m in length - and
2 fast intervention aluminium crewboats.
In 2004, Constructions M'chaniques de Normandie
(CMN) have delivered a patrol boat to the French
Maritime Administration and have under construction a
corvette for the Emirates Navy within a programme of
six boats for the same client, and two motor yachts of
respectively 58 and 42.6 m in length.
|

|
Fast ferry
Artist impression of a 450 seats fast catamaran
ordered by Conseil G'n'ral de la Vend'e at the
Norwegian shipyard Fjellstrand for a service
between Fromentine and Ile d'Yeu
|
Germany
There are some twenty shipyards in Germany of which
about fifteen build almost exclusively containerships
between 800 and 4,000 teu. Meyer Werft, reputed for its
cruiseships, has even filled up its orderbook with a
series of four containerships of 1,500 teu. Amongst the
major shipyards, only Flensburger and Lindenau are
specialising in other types of ships such as Ro-ros and
Ro-paxes on one hand, product tankers on the other.
German builders have naturally benefited from the
enormous demand in the containership sector and, above
all, from the sustained interest for feeders, a size
which the three large South-Korean yards have
abandoned. They have also been able to offer prompt
delivery dates which are particularly sought after by
German investors (KG) whose proximity helps business
relationships.
The orderbook of German shipbuilders has gone from
2.3 to 3.1 million gt between year-end 2003 and
year-end 2004. Germany occupies the 2nd position in
Europe behind Poland and is ranked 6th in the world.
|
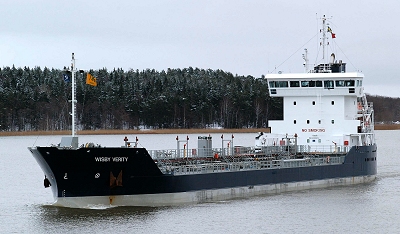
|
Wisby Verity
7,600 dwt, delivered in July 2004 by Ferus Smit,
owned by Wisby Tankers of Sweden and on long-term
charter to Preem Petroleum.
|
Italy
There are some fifteen shipyards or building sites
in Italy. Cruiseships, Ferries, Ro-ros and Car-carriers
form the core of Italian production (Fincantieri,
Visentini). But there are also some very good
specialist shipyards such as De Poli or Di Pesaro for
chemical carriers, gas carriers and small bunker
tankers.
Italian shipyards have been particularly successful
in obtaining over half of the new orders for Ro-ros,
Ro-paxes and Ferries. Fincantieri, for its part,
succeeded in capturing 6 out of the 13 cruiseships
ordered in 2004 and has confirmed its place as the
European leader in the cruise sector.
The orderbook of Italian shipbuilders has gone from
1.25 to 1.8 million gt between year-end 2003 and
year-end 2004. Italy holds the 4th position in Europe and
the 8th position in the world shipbuilding ranking.
Spain
There are still some twenty shipyards or sites in
Spain, but the question that has to be asked is for how
much longer?
Spanish shipbuilding is in a crisis and is going
through a drastic change, somewhat in the same mould as
in other European countries during the 1980s and 1990s.
European authorities have told Spanish authorities
to put an end to certain practices which they consider
to be contrary to EU regulations. In particular, they
have asked Izar to reimburse subsidies received in 1999
and 2000. Under these circumstances, Izar, who did not
have any new order in 2003, has not been authorised to
take on any new business in 2004. The separation
between military and commercial sites should be done
and be followed with the privatisation of the latter.
The Spanish shipyards' situation remains fragile on
the overall. It is a shame that Spain has not been able
to benefit from the revival in the newbuilding market.
However, this allow them to propose very prompt
delivery dates and would put them in a position to take
advantage from the healthy sales prices in 2005.
The Spanish shipbuilding orderbook has gone from
500,000 to 135,000 gt between end 2003 and end 2004. It
is one of the few countries in the world with a
shipbuilding tradition that has seen its portfolio
decline this year.
|
Finland
There are three construction sites in Finland,
which however work under the single banner of the
Aker Yards group. In September, the Aker group
announced the merger between Kvaerner Masa and
Aker Finnyards, under the combined name of Aker
Finnyards Inc. This new entity will employ 4,500
people of which 1,000 on the Rauma site, 2,000 in
Turku and 1,250 in Helsinki.
Cruiseships, Ferries, and Ro-ros are the
mainstay of the Finnish production. The recovery
in these sectors has helped them and their
orderbook has moved from 400,000 to 550,000 gt
between year-end 2003 and year-end 2004.
The Turku site (ex Kvaerner-Masa) picked up in
2004 the order for a second 'Ultra Voyager-type'
cruiseship, 160,000 gt and 3,600 passengers, for
RCCL. The Helsinki shipyard (ex Aker-Finnyards)
was awarded the order for an ice-breaking
containership for Russian account and has signed a
letter of intent to build a cruiseship for NCL.
Finally the Rauma site obtained the order for
three carriers specialised in the transport of
forest products and a 2,800 passenger ferry.
Finnish shipyards have an uncontested know-how
in building ships for navigating in polar
latitudes, and should therefore benefit from the
growth in this traffic with the Russians.
Denmark
The last major Danish shipyard Odense Lindo
keeps on building series of over-Panamax
containerships for the account of its main
shareholder, the AP Moller group, which has become
the only client of this yard. In the current
context, to be the owner of a shipyard when you are
also ship owner is a clear advantage.
Netherlands
There are still some fifteen Dutch shipyards,
whose production is mainly concentrated on
building general cargo ships, multi-purposes,
small containerships, small product tankers and
offshore supply vessels.
The Dutch shipyards' orderbook has gone from
280,000 to 490,000 gt between year-end 2003 and
year-end 2004.
After a difficult year 2003, which saw the
closure of a number of sites, Dutch shipyard
workers held massive protest meetings at the
beginning of 2004 to attract the attention of the
authorities. The government, in turn, conceded a
form of temporary defence mechanism, while they
also benefited from the market upturn.
The Dutch shipyards operate largely by
sub-contracting hulls to Romania, Ukraine, Poland
and Turkey, without which they could not be
competitive today with small yards in China,
Korea, Turkey, Romania, or Poland. Some shipyards
even succeed in having a full orderbook without
doing any construction in their own sites in the
Netherlands, this of course, creating other
problems.
Norway
Norway has some fifteen shipyards. Their
production is largely concentrated on offshore
units such as PSV or AHTS. There was also
the rare order at the end of the year for an
orange juice carrier of 40,000 dwt at Kleven Werft.
Norwegian shipyards also sub-contract a lot of
hulls in Eastern Europe and have succeeded in 2004
to renew fruitful relationships with some Russian
shipyards. Thus, Fosen has become associated with
Baltiyskiy Zavod for building Ro-ros for the
account of Stena, while Kleven Maritime has joined
up with Sevmash for a series of coated chemical
carriers for the account of Odfjell.
Portugal
The last large Portuguese shipyard, Viana do
Castelo, is currently building a product tanker of
19,000 dwt for the account of the French owner
Fouquet-Sacop and another of 14,000 dwt for the
Finnish owner Fortum, as well as two coastal
passenger vessels for a domestic account. They
also have an agreement to build a significant
series of vessels for the Portuguese Navy.
Poland
Poland has four main shipyards whose production
is largely geared to build containerships,
open-hatch bulk carriers, car-carriers and Ro-ros.
The orderbook of Polish yards has gone from 2.5
to 3.3 million gt between year-end 2003 and
year-end 2004. Poland keeps its 1st place within
Europe and the 4th place in the world ranking.
Poland, now part of the European Union, has to
progressively abide by its regulations. In
particular, the shipyards in Gdynia and Gdansk,
which have benefited from state funding, will see
their capacity being limited to 390,000 cgt over
the next ten years.
Polish yards, which have experienced serious
financial difficulties, have given priority to
their traditional clients and to build series of
existing, proven designs thus reducing their
risks.
Croatia
There are five shipyards in Croatia whose
orderbook has gone from 1.5 to 2.7 million gt
between year-end 2003 and year-end 2004. Croatia
occupies the 3rd place in Europe and the 7th place
in the world.
Croatian yards have largely benefited from the
demand of product tankers and of car-carriers. The
orderbook of Treci-Maj and Uljanik are full until
mid-2008, Trogir and Split are full until early
2009.
Turkey
Apart from a few sites, Turkish shipbuilders
are mainly located in the bay of Tuzla, located
some thirty kilometres from the heart of Istanbul,
in Anatolia. There are about 35 shipyards next to
each other in a semi-circle with a radius of about
1,000 m. Currently it is brimming with activity.
Most of the ships under construction are less
than 10,000 dwt. Between 2003 and 2004, the five
biggest builders in the bay took on orders for
ships between 15,000 and 20,000 dwt. One of them,
Celik Tekne, is even building a sophisticated
product-chemical tanker of 25,000 dwt for delivery
in 2005.
These shipyards display a remarkable dynamism
and special ingenuity. They seek to increase their
building capacity by constructing new berths, new
lifting procedures, new workshops and study
numerous expansion projects.
Current production is mainly concentrated on
product tankers and chemical carriers (including
some stainless steel units), but there are also
cement carriers and containerships in the
orderbook. A number of hulls bought in Romania or
in Bulgaria have been towed there in order to be
fitted out and finished.
Most of the Turkish shipyards' clients are West
European owners, but also West European shipyards
who sub-contract hulls. Some Turkish owners have
contributed in the form of orders for which they
basically act as shipbuilders: they build their
own ships using the yards' facilities but
supplying the design, steel and equipment.
The orderbook of Turkish yards has gone from
250,000 to 365,000 gt between end-2003 and
end-2004
Romania
Romania has six shipyards. The revival of
Romanian shipbuilding which was already firmly in
place has been consolidated by the strong demand
throughout the year 2004, both for complete
vessels as well as sub-contracted hulls from West
European shipyards.
The orderbook of Romania yards has gone from
230,000 to 550,000 gt between year-end 2003 and
year-end 2004.
Romanian production is diversified and consists
of offshore units (PSV), product tankers, Panamax
tankers, and containerships. German owner Gebab
has ordered six containerships of 4,800 teu at
Daewoo Mangalia.
This excellent performance is largely due to
the strategic investments made by three foreign
groups: Aker, Daewoo, and Damen. These Norwegian,
Korean, and Dutch companies have supplied their
own know-how and the benefit of their reputation
to the respective shipyards: Aker Tulcea, Aker
Braila, Daewoo Mangalia and Damen Galatz.
|
Russia
There are ten shipyards in Russia, whose
orderbook has doubled from 350,000 to 615,000 gt
between year-end 2003 and year-end 2004.
They have been able to benefit from
considerable domestic orders. Baltiyskiy Zavod has
thus been given the order for a tanker of 75,000
dwt for Rosneft. The foreseeable increase in oil
exports from this country and the need for
ice-class ships capable of navigating in polar
latitudes should probably help feed Russian
shipyards with new orders.
Russian shipbuilding has also been able to take
advantage of the world demand and the programmes
of cost-cutting by European yards in the form of
sub-contracting. Baltiyskiy Zavod is going to
build in co-operation with Fosen shipyard two
Ro-paxes for the account of the owner Stena.
Sevmash in conjunction with Kleven Maritime will
build a series of eight chemical carriers of
40,000 dwt for the account of Odfjell.
|
United States
The American shipbuilding industry is concentrated
on its national market. Despite a strong
rise in construction costs and a search for new
capacities, American shipyards remain too expensive and
have not been able to take advantage of the current
situation. As an example, Kvaerner Philadelphia (Aker
Yards) have only sold four containerships of 2,600 teu
since 2002, at a unit price of roughly $ 70 million,
namely more than double the price inked with Asian
yards.
Avondale and National Steel (NASSCO) are the two
large commercial American shipyards where tankers of
140,000 and 185,000 dwt are under construction. They
belong to American shipping defence companies,
respectively Grumman and General Dynamics, but have not
registered any new merchant ship order this year.
New orders for merchant ships are scarce, except for
the offshore industry. Besides, a part of the homeland
security budget is dedicated to the building of a
number of ships for the account of the U.S. Coast
Guard, which should keep the civil shipyards busy for
several years.
|
Prospects
|
|
2004 has been an exceptional year on many aspects. An
unequalled growth, unprecedented freight rates,
unsurpassed second-hand ships' values, a record world
orderbook and raw materials (oil, coal, steel) at
historical highs.
Will the orders intake remain as high as over
the past two years? Will the price of ships continue to
climb? Are the markets able to absorb the capacity of
such an orderbook?
Numerous factors suggest a continuation of this
trend due to the enormous requirements of China, to
which can be added those of India and other emerging
countries. Some believe that the strength of the
freight market could last through 2005 or even beyond
into 2006. Others claim that the
engine of the Chinese economy will keep on running at
full speed until the Olympics Games of 2008, or even
the Universal Exhibition in Shanghai of 2010. Finally,
the most optimistic seems to detect economic miracle
signs in China of an identical cycle to that of the
post World War II in the Western world.
Volumes
Whereas more than 110 million dwt of ships were
ordered in 2003 and builders' portfolios were already
spread out for over three years, the continuation of
this trend in 2004 was surprising.
With an economic development and a world trade
superseding the most optimistic forecasts, and as a
corollary an unprecedented rise of freight rates and
the improvement of owners' financial standing, these
are the underlining explanations for the volumes
ordered.
First, shipyards became euphoric with their
commercial success, but they progressively realised
that the increases in newbuilding prices obtained in
2003 were hardly sufficient to cover the rise in their own costs. They discovered, with
dismay, that they had taken enormous risks and that in
fulfilling existing contracts they could jeopardise
their financial results.
Builders could well exercise additional caution in
2005 by not agreeing to take on any new orders except
at substantially higher prices, especially as they have
time on their side. This could cause owners to slow
down as well, as they have taken on commitments over
the next three years themselves (165 million gt on
order).
Prices
Shipbuilding prices in 2004 reached new levels,
equalling and in some cases surpassing the records
obtained at the beginning of the 1990s (in actual
values). Owners can reasonably ask themselves, in such
heady time, if they might not soon encounter a decline.
However, one should keep in mind that $ 100 million
in 2005 is worth considerably less than the same $ 100
million in 1991 (in current values) and meanwhile the
price of steel has risen.
The analysis of the cycle that shipbuilding
experienced in the 1980s is instructive. In 1985, a
VLCC of 250,000 dwt would have been contracted for
around $ 35 million at the Asian shipyards. The upward
cycle then followed a six year trajectory, into the
beginning of the 1990s, to the point where the same
single-hulled VLCC would have cost around $ 90 million.
At the same time, the price of a 300,000 dwt
double-hull VLCC reached the $ 110 million region.
If we expect the current upward cycle to las as long
as the previous one, there is no doubt that newbuilding
prices still have some margin to go up. Much will
depend on the further development and stability of the
dollar exchange rate, which remains a serious issue. We
can also draw some comfort in the extrapolation of most
economists, whose sentiments are that the dollar is not
about to appreciate substantially against the
currencies of the main shipbuilders.
Of course we would like to be able to predict
newbuilding prices evolution and we would like to know
if an eventual drop could send us again towards the
very low levels seen in mid 2002.
Given the size of shipyards' orderbooks, the
pressure placed on an already strained raw materials
markets and world growth forecasts, it seems probable
that newbuilding prices will continue to climb during
2005 and 2006 as long as steel prices do not drop.
There is nevertheless reasons to be careful about
the enormous building capacity that China will put on
the market as from 2008 / 2009. This, coupled with the
steady productivity improvement achieved by the
Chinese shipbuilding industry, may start to break this
delicate balance. The outcome will then depend to a
large degree on the capacity of resistance offered by
the Japanese and South-Korean shipbuilders.
|
Shipping and Shipbuilding Markets in 2004
I N D E X
|