The Shipbuilding market in 2003 (2) |
|
Analysis by country |
Asia |
- Korea |
2003 was
a new record year for Korea, which asserts its world
leadership in the shipbuilding industry.
The Korean shipbuilders' orderbook went from 25 to 48
million tons between end 2002 and end 2003. Sale
targets of shipyards set at the beginning of 2003 were
already met by the third quarter and then surpassed
|
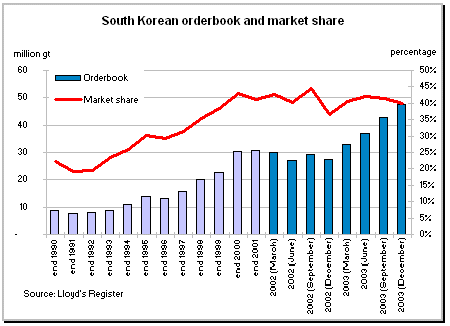
|
Korea's progress is
extraordinary when compared with the figures of
the world orderbook, which ten years earlier stood
at 36 million gt, or again with their orderbook at
that time which was 10.9 million gt. It shows the
impressive vitality of the Korean shipbuilding and
its response to the evolution in demand.
Unlike China, there have been
no new docks recently installed, but an optimisation in
their production capacities has contributed to this
dramatic growth. Docks designated for offshore units
have been partly used to build cargo vessels.
Bottlenecks in the building chain are constantly
examined with special attention and appropriate
measures are taken to remedy the situation. Recourse to
outsourcing and especially of hull blocks is growing.
Builders are also opting for
other methods, used especially in the offshore and in
certain Chinese shipyards, by constructing ships on
open land.
The big Korean shipyards
(Hyundai Heavy Industries, Daewoo Shipbuilding and
Marine Engineering, Samsung Heavy Industries, Hanjin
Heavy Industries) hesitated throughout the year to
commit their docks over and above a period of three
years but the pressure was too strong. They gave
priority to the very big ships, essentially
containerships, tankers and LNG carriers, and abandoned
the bulk carriers, even Capesize, apart from some
exceptions.
The three shipyards
specialising in building product tankers of 37,000 dwt,
47,000 dwt, and Panamax (Hyundai Mipo, STX, Shina)
accumulated a record number of orders.
The small Korean shipyards
also attracted a number of Western owners who at other
times would have ordered in Europe. In this respect
there was the order of two stainless-steel chemical
carriers by the Danish owner Wonsild with INP.
Korea's market share in the
three types of ship is respectively 3% for the bulk
carriers, 50% for tankers, and 64% for containerships.
|
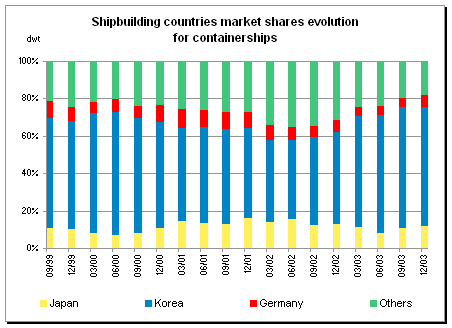
|
- Japan |
2003 was also a new record
year for Japan confirming its second place in the world
ranking.
Japanese shipbuilders'
orderbook went from 24 to nearly 38 million tons
between end-2002 and end-2003. New orders represented
more than 26.7 million tons this year as against 15.1
in 2002.
|

|
In 2002 Japanese
builders kept pace with Korean builders in terms
of new orders due to their dominant position in
the bulk carrier market.
2003 figures underline
the dynamism of Japanese shipbuilders but also of
Japanese owners who are their main and often
exclusive clients, which drive this island
nation's ambition not only to maintain but also to
develop their shipbuilding industry in a highly
industrialised country. They show that it is still
possible to build standard ships at market prices
with a work force even more expensive than those
of their competitors (Korea and China).
Japanese shipyards are looking
to adjust to demand and to free themselves from
constraints that were imposed in the past to limit
overcapacity. Some shipyards have been given
authorisation to build ships of bigger tonnage and to
expand their docks. Japan has at hand a number of sites
which were mothballed during the crisis of the 1970s
and 1980s that can now be reactivated.
It is very likely that this
practice could be extended in the case of sustained
demand.
|
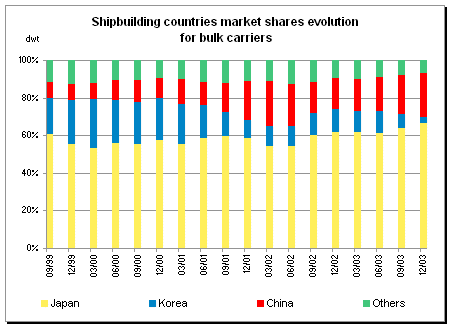
|
- China |
2003 was also a record year
for China which confirms its third place in the world
ranking. The orderbook of Chinese shipbuilders went
from 9.1 at the end of 2002, to more than 15 million
tons one year later. .
|
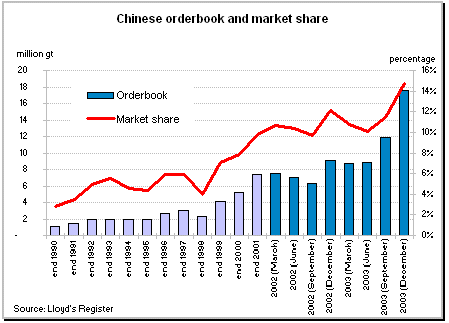
|
Chinese shipbuilders
surpassed their objective of 10 million gt before the
date that they had fixed (2005), despite the SARS
epidemic, which hit the country in the second quarter
of the year and slowed down numerous projects.
Expansion in Chinese
shipbuilding is continuing. New large shipyards are
under construction (e.g. Nantong Rongshen), while
existing yards are expanding or modernising their
production facilities. Some yards located in urban
areas are being displaced where facilities are
modernised and capacity increased (e.g. Shanghai
Shipyard to Chong Ming island, Jiangnan Shipbuilding to
Chang Xing island, Qingdao Beihai to Haixiwan, etc.).
Finance for this capacity
expansion is coming from various sources. Funds
provided or loans guaranteed by central, provincial or
city governments seem to account for a significant
amount of the investment in shipbuilding, however
direct foreign investment and private domestic funds
are now becoming more and more active, especially in
the privatising of former government controlled
shipyards.
China is thus becoming
equipped with gigantic shipbuilding facilities, capable
of competing in the future with the largest Japanese
and Korean shipyards. China's ambition is to become
number one in world shipbuilding before 2015, which is
tomorrow.
|
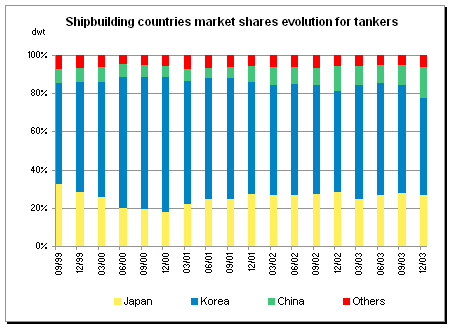
|
China has even surpassed its
own expectations and surprised its previous critics.
Chinese yards today build almost every type of ship,
even if they are, from time to time, delivered with
some delay. The latest ships produced in China, which
can be sometimes extremely complex, are trading well
worldwide and are witness to the progress achieved over
the last few years.
Chinese shipbuilding has
however seen some failures, the best known being the
case of the Jiang Yang shipyard but even in this case
the new wave of private investment has illustrated the
trend of the private sector taking over where previous
government management failed. The year 2003 saw a new
identity, 'Yangzhou Dayang Shipbuilding' rising from
the ashes of the defunct Jiang Yang shipyard.
Shipyards have been able to
enjoy a great degree of liberty over the last years,
but some have at the same time encountered some losses,
hence a closer scrutiny from the highest levels in the
commercial policy of these yards is being implemented.
Perhaps, more than elsewhere,
due to a lack of some 'old clients', Chinese shipyards
have been more opportunistic, which has sometimes
irritated some owners.
The fixed exchange rate
between the yuan and the dollar has clearly been a
considerable advantage this year for Chinese builders,
offering them a distinct competitive edge over their
Japanese and Korean rivals. Nonetheless, this fixed
parity does not completely protect them when the yen,
euro, and won appreciate against the dollar as they
need to buy numerous supplies and base products outside
China. This is why Chinese builders are pressing the
authorities to develop domestic production of ships'
design and equipment, as Japan and Korea did in the
past. The very strong growth in the Chinese economy and
the enormous demand for steel products have produced a
cascade of price hikes for steel-plates and steel
sections, increasing builders' costs and reducing their
margins.
Confronted with the trade imbalance between the US and
China, Washington is pressing Beijing to re-value its
money. The depreciation of the dollar compared to other
main currencies might lead the Chinese authorities to
consider raising the exchange rate of the yuan against
the dollar or to let their currency float, even
partially, which of course would have an impact on
Chinese shipbuilding.
|
- Taiwan |
Like other shipyards in the
Far East, Taiwan's state shipbuilding group, CSBC,
following a deep and painful restructuring programme,
has filled up its orderbook in 2003 particularly with
containerships and some Panamax or Capesize bulk
carriers. The CSBC orderbook (split between two sites
located in Kaohsiung and Keelung) has almost doubled to
achieve roughly 2 million tons (1.2 million tons end
2002) allowing Taiwan to hold sixth place in the world.
The privately controlled
Ching Fu Shipbuilding is also holding a full orderbook
and has establishing itself as one of the emerging
leaders in fishing vessels and other specialised types
below 15,000 dwt.
|
- Other countries in the
Indo-Asian zone
|
We should mention the renewed
interest this year for shipbuilding, in countries that
should be able to benefit from the huge demand and
higher prices. History shows that in such periods
owners generally go out to encourage new suppliers in
order to obtain reduced prices or simply earlier
deliveries.
To illustrate this point we
can cite emerging capacity and further development of
shipbuilding in Vietnam, India and Iran, the latter
founded for domestic requirements is now attracting
international buyers.
In the Philippines, where the
Japanese shipyard Tsuneishi established the subsidiary
base at Cebu in 1994 to concentrate on the construction
of Handymax bulk carriers, production rose from 7
deliveries per year in 2001 to 10 deliveries achieved
in 2003 of the Cebu standard design 'Tess 52'. With
this full orderbook, an investment programme is already
being implemented to reach an annual production of 14
newbuildings in the next few years.
|
Europe |
New orders are in sharp
decline. The total orderbook for Western Europe is
still shrinking, dropping from 6.7 million gt in
December 2002 to 6 million gt by the end of 2003. The
fall in market share of West-European shipyards from
8 % to about 5 % is even more spectacular, but it is
also proportionally due to the considerable increase of
the Asian shipyards' orderbooks.
West European shipbuilding at
the beginning of this decade underwent a downscale
compared to the 1990's, when the orderbook was hovering
between 8 and 9 million gt.
By simply drawing a straight
line, we could forecast that European shipbuilding
would disappear in the coming years, but nothing is as
uncertain as extrapolation.
If we try to analyse this
evolution we can see that from the beginning of the
1990's most European shipyards have implemented
cost-reduction schemes:
-
production outsourcing
(carpentry, electricity, air systems, pipes,
outfitting, assembly),
-
reducing their management
staff and often buying their designs,
-
rationalising procurement,
-
sub-contracting steel blocs,
or consigning entire hulls to East European countries,
such as Poland, Romania, Turkey, Russia, Ukraine,
complicating at the same time the management of this
sub-contracting,
-
sub-contracting to the same
yards the outfitting of ships, which are now almost
completely built abroad.
They have done away with the
superfluous but sometimes also with the essential
skill, and particularly human resources that make up
the intellectual capital of shipyards.
Today European yards are
organised to build ships of small and medium sizes
(less than 40,000 dwt), which have been progressively
abandoned by the large Korean and Japanese shipyards,
and are being battered by the strength of Chinese yards
now interested in building all types and sizes of
ships.
To a large extent, European
shipyards have also lost their subsidies. At the end of
2000, they had filled up their orderbooks for three
years in order to benefit from the maximum authorised
in the EU, up to 9 %. The end of this mechanism
increased the price differential with Asian shipyards
and, whereas some clients were still prepared to pay a
little more to stay in Europe, they progressively left
the area due to an ever-growing disparity. For some
shipowners building in Europe became an unaffordable
luxury item.
European shipyards have also
more recently been handicapped by the level of the
euro, in a market where ships' values are most of the
time expressed in dollars.
Certainly
there are areas of excellence in Europe, such as the
building of cruise-ships, ferries or other passenger
ships, but will there be a sufficient number of orders
in these sectors to allow full employment of these
facilities?
|
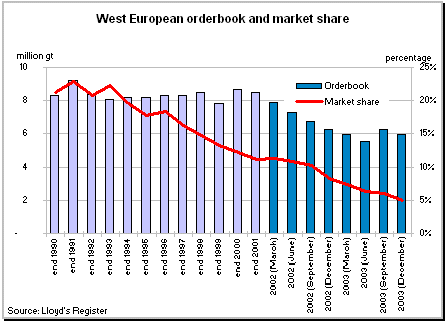
|
European shipyards have
unfortunately today structural handicaps compared to
their Korean, Japanese, and Chinese counterparts. For
political, social or economical reasons, they have not
been able to restructure their facilities. Newbuilding
sites remain widespread all over Europe and can not
compete with the Korean giants. Fincantieri and Izar,
which have several domestic sites, have not even merged
or closed any facilities. For lack of means, they have
not been able to invest in their yards as the Koreans
and Chinese builders have done on a massive scale. On
top of that, the tax burden, social costs and
administrative constraints add some weight to the bill.
In industrialised countries
like Japan and Korea, net salaries are on a par or even
higher than those of European workers, however,
differences in social expenses and the number of
working hours make man-hour cost much more expensive.
Therefore, on the basis of identical costs for
procurement and equal man-hours to build a ship, there
still would be a gap between Korean or Japanese and
European builders to the detriment of the latter.
An alternative policy could
have been to favour the closure of some sites in Europe
and the merger of some of the remaining capacities.
Will there be a turnaround?
One must hope so and also that it comes quickly as
European shipyards are continuously laying off workers
and even some closing down. A further new reduction of
West European production capacity is again to be
envisaged for this year.
Notwithstanding the above,
West European shipbuilders have today good cards up
their sleeves, as they could offer earlier delivery
dates and should obtain a premium above current market
prices on that basis.
|
-
France
The orderbook of the major
French shipbuilders has dropped from 553,000 tons end
2002 to 380,000 tons end 2003.
After having signed a
contract for the construction of a LNG carrier of
74,000 cbm with Chantiers de l'Atlantique in 2002, Gaz
de France decided this year to order another LNG
carrier of 153,000 cbm, which will as well be a
membrane type, equipped with an advanced propulsion
based on a combined diesel-gas-electric engine. This
propulsion offers two advantages to the owner:
important energy savings due to a lower consumption and
an additional cargo capacity for similar dimensions.
Chantiers de l'Atlantique
have also received an order for a ferry of 1,900
passengers, 700 cars and 2,000 lane-meters for the
account of Sea France.
Demand for cruiseships
remained weak over the last three years and prospects
remain modest in the short term. Chantiers de
l'Atlantique are currently taking measures to adjust to
this new environment, not having been able to obtain
any new cruiseship orders since 2000. They have
delivered four cruiseships in 2003, including the
'Queen Mary 2', the biggest liner ever built,
demonstrating the excellent performance of the yard.
Chantiers de l'Atlantique
hope to be able to build military ships like other
shipyards elsewhere in Europe. Without a special
agreement, this is a rare event in France since
military shipbuilding is restricted to naval yards.
However a joining of forces could benefit all the
parties: Chantiers de l'Atlantique possess a highly
efficient organisation and can propose economically
viable solutions which should in co-operation with naval
yards, reduce the cost of their ships. The French Navy
could thus satisfy its needs more easily and the French
government would reduce its expenses.
With the
progressive downsizing of the deep-sea fishing fleet,
planned by Brussels, we should note that since the
delivery of the 'Ulysse', Piriou Shipyards in
Concarneau, have managed to diversify and propose a
large range of products from AHTS, PSV, tugs and some
others innovative service ships, either for some French
interests or foreign clients.
Piriou
Shipyards still propose their traditional trawler,
seiner and other fishing boat designs. In this highly
competitive context, the yard has been able to develop
its client base and sign a number of new contracts.
They also developed a new building facility on
Mauritius which reinforces their presence in the
region.
The situation at
Constructions Mecaniques de Normandie in Cherbourg is
rather different as they still have a strong workforce
of about 400 employees and an order backlog which
suffers from a lack of private clients. The latest
order for a series of 6 corvettes from the Emirates
Navy at the end of the year, of which only the first
one will be built at Cherbourg, has brought some fresh
life to the shipyard until 2007. The French Coast Guard
has a 52 metres long patrol boat on order at the yard.
Some yachts and sailing ships have to be added to this
orderbook which is still not completely full.
|
-
Germany
German shipyards have
benefited from the tremendous demand for
containerships. Whilst Korean shipyards were
concentrating on very large container carriers, German
yards received orders for 54 new ships mainly in the
2 500 / 3 500 teu size range as well as feeders of
smaller size. For reference, in 2001, German yards
signed up orders for 46 containerships of over 1 000
teu. In 2002, this figure was divided by three.
They have benefited from the
lack of interest for these smaller sizes from Korean
yards, but also from the proximity with their buyers
(all Germans), and finally from an overflow of orders
from Asia onto Europe, which, despite higher prices,
has been able to offer earlier delivery dates in the
second half of 2003.
Meyer Werft received two
orders for cruiseships of 93,000 tons for the account
of their traditional clients Star Cruises / NCL as well
as a new passenger-ferry for Indonesia.
Flensburger has been
specialising more and more in ro-ros and Lindenau
continued its success in the tanker sector securing
orders for 5 product tankers of 32,000 to 34,000 dwt.
As to the other shipyards
which diversified in other types of ships, times are
becoming more difficult. Flender Werft and SSW have
closed down. Elsewhere, reduction of personnel and
other plans (early retirements and layoffs) are going
on.
Germany
occupies the second place in Europe behind Poland and
ranks number 5 in the world.
|
-
Italy
Italian builders were
penalised by the prevailing weak demand for cruiseships
and passenger liners.
Nevertheless, Fincantieri was
awarded one of the 4 orders for cruiseships placed
in 2003 and carry in their orderbook 8 cruiseships to
be built in three different construction sites. They
have also received orders for ro-ros and ferries for
their Ancona, Napoli and Palermo facilities from
Italian owners. Italy occupies 4th rank in
Europe and 8th in the world.
|
-
Spain
In 2003, Izar, the Spanish
state shipbuilding group, successfully delivered their
first three 138,000 cbm LNG carriers and should deliver
this year the two remaining ones, out of an order for
five ships signed in 2000. Izar clearly hopes to
continue in this niche against very fierce competition
from Asia.
Unfortunately with the
exception of Barreras, Spanish shipyards succeeded in
taking very few new orders in 2003. In addition,
European authorities have requested Spanish authorities
to put an end to certain arrangements favouring
shipping investment, which were considered to be
contrary to the Community regulations.
|
- Finland
Finnish shipbuilders also
suffered from the poor demand for cruise and passengers
ships.
Kvaerner-Masa Yards have
however gained the order for the biggest cruiseship
ever to be built (160,000 gt) for the account of Royal
Caribbean. They have also landed the order for very
sophisticated ice-breaker ships for Russian account.
Finnish shipyards have an
indisputable expertise in building ships capable of
navigating in ice conditions and their geographical
position is an advantage. They should benefit from the
Russian growth and renew their links with an economic
partner who had rewarded them before the fall of the
Soviet Union with numerous orders.
They could also take
advantage from the economic development of the Baltic
states which are about to join the European Union.
|
- Denmark
Odense Lindo, the last major
Danish shipyard, continues to build a series of large
containerships, of which the last version should
approach the 10 000 teu size. These containerships will
then be operated by the shipping branch of the A.P.
Moller group, which was the first owner to invest in
large containerships. Together with MSC, they are the
sole owners in the world who have their own private
terminal capable of discharging ships with beams up to
21 / 22 rows of containers
|
- Netherlands
2003 was a particularly
difficult year for Dutch shipyards. After the closure
of Tille at the beginning of 2003, van der Giessen-de
Noord, specialised in the building of ferries, decided
to cease their activities in shipbuilding, just after
the delivery of the French ro-pax 'Pascal Paoli'. One
of the building sites of another yard, Bijlsma, also
had to close down.
Dutch shipyards, still very
active in the sector of small ships, owe their survival
to their capacity for innovation. Hulls are largely
subcontracted out to Romania or Ukraine, before being
repatriated for outfitting. Dutch yards are still
strong in the building of offshore support ships,
dredgers, small cargo vessels and small petroleum
product and chemical carriers.
Dutch shipbuilders have
suffered badly from the aggressive competition of
Chinese shipyards for similar types of ships. With only
slighlty more than 300,000 tons on order at the end of
2003, the Dutch shipyards are now close to the bottom of the
world ranking.
|
-
Norway
The merger in 2002 of two old
rival yards Aker and Kvaerner gave birth to a group
with twelve yards in Norway, Finland, Germany, Romania,
Brazil and the USA, employing 13 500 people and having
a turnover of around 20 billion Norwegian crowns.
2003 was a very difficult year
and the orderbook of Norwegian shipyards dropped
significantly. The shipyards suffered from the
appreciation of their currency. Now specialised in the
offshore sector, the overall tonnage on order at
Norwegian shipyards does not weigh much in the world
shipbuilders' ranking despite that the value of each
ship is often very high.
|
-
Poland
Polish yards which had
encountered important financial difficulties in 2002
necessitating restructuring and recapitalisation, were
on the rebound in 2003. Their production is largely
orientated on containerships, open-hatch bulk carriers,
car-carriers and ro-ros.
Poland occupies the first
rank in Europe and fourth rank in the world with about
2.5 million gt at the end of 2003. Poland's entry into
the European Union could be a new stimulus to growth
but the shipyards will probably have to face a
progressive increase in their salary costs.
|
-
Croatia
Croatian shipyards have
largely taken advantage from the demand for product
tankers and car-carriers. The five main shipyards
Split, Trogir, Kraljevica, 3 Maj and Uljanik are full
up until 2007. They place themselves often with ships
slightly more innovative than those built in Asia.
Trogir is finishing a series of 6 product tankers of
47,000 dwt fitted with a two-engine propulsion and one
crankshaft. Split has been awarded the order from Stena
for a series of 6 P-Max type tankers.
At the end of 2003, Croatian
shipyards occupy 7th place in the world with
about 1.5 million gt on order.
|
-
Turkey
Turkish shipbuilding with its
numerous shipyards benefited from the demand for small
oil product carriers and chemical carriers from
domestic and European owners. Domestic owners are also
very dynamic. Turkish yards are also used to take
subcontracting works from West European shipyards. With
nearly 300,000 dwt on order, Turkish shipyards are now
at a level comparable to the Netherlands shipbuilding
industry.
|
- Romania
Romanian
shipyards have benefited from significant direct
foreign investment and management from experienced
international shipbuilders (Aker, Daewoo, Damen, etc.)
and have been able to take advantage of the overflow
from Asian yards. They managed to attract orders which
could have gone to Korea in other circumstances. Thus,
Constanza signed contracts for two product tankers of
37,000 dwt and Daewoo Mangalia for two Panamax tankers.
In the meantime 2003 saw a significant increase in both
volume and value of the subcontracting of hulls of a
diverse range of vessel types including offshore and
container vessels for a number of West European
shipbuilders.
|
-
Russia
Russian shipbuilding should
also logically draw benefits from the world demand and
the congestion of Asian yards, with sites being able to
offer earlier delivery dates. They could also take on
domestic orders in view of the predictable increase in
oil exports from this zone, and the pressing need for
ships of suitable ice class. Its industrial
infrastructure however needs to be enhanced.
|
United States |
The American shipbuilding
industry has consolidated its position this year and
has maintained its 9th place in the world
with around 0.7 million tons at the end of 2003.
However, American yards protected by the Jones Act, are
not really able to be in the market at competitive
prices.
In 2003 the Aker-Kvaerner
group saw its first newbuilding delivery from their
Philadelphia shipyard of a 2,600 teu containership for
the US flag owner MatsonNavigation Company.
This is the first of a two-ship order and each vessel
was reportedly priced at $ 110 million (owner's costs
included). There was originally a lot of hope that by
taking on the Philadelphia shipyard that the
Aker-Kvaerner group could bring it back into the
international shipbuilding market, but today it is
unable to ensure a sufficient workload, due to the
pricing distortions of the Jones Act environment (US
built - US flag - US crew).
Nassco of
San Diego is still working on 4 Suezmax tankers of
185,000 dwt for the account of BP, bound to trade
between Alaska and the US West Coast, also under the
Jones Act regulation. However it should be noted that
this activity is secondary to Nassco's many contracts
for the US Navy.
|
Prospects |
The very strong demand for new tonnage in 2003 and the
reversal of what has traditionally been a 'buyers'
market to a 'sellers' one was hardly anticipated. Will
this trend continue?
We can reasonably think it
will, at least for 2004 and this is for several reasons:
-
Inflation often breeds on
itself: the enormous demand is causing at the moment
substantial increases in procurement costs and
especially in steel plate prices. Despite increases in
the price of ships, it is not certain that yards will
improve their margins. In these conditions, it is
likely that shipbuilders will maintain a policy of
price increases, which in turn could motivate owners to
invest today rather than tomorrow.
-
These owners may also
consider that prices from the yards, for a large
variety of ships, are still below the historical highs
reached at the beginning of the 1990s, and thanks to
low interest rates it is reasonable to invest.
-
Prices have broken through
new limits, rendering the reference benchmark prices of
the past five years obsolete. The former equilibrium
has been broken and we have entered a new cycle. Given
the current situation with shipyards, suppliers, raw
materials and energy, it is fairly certain that
newbuilding prices will remain at high levels for
several years.
There will be however a
correction to this trend as these price increases pose
several problems as to the real value of the assets and
their financing. Owners can
ask themselves if it is reasonable to order ships for
delivery in four years time. The ratios of
ships on order versus active fleet may also be a cause
for concern: how will the market absorb this overflow
of tonnage?
The enormous shipbuilding
capacity that China is putting on the market and its
ambition to become the leading shipbuilder in the world
within 2015, will certainly meet some strong resistance
from Japan and Korea.
All of this is part of the
'common' history of the shipping industry, euphoric
periods being often followed by more or less deep
depressions. We can see some similarities between the
current dry bulk freight market evolution and the stock
exchanges excesses in the 1999 to 2000 period, before
the bubble burst!
Adjustments are already taking
place, since the cost of shipping becomes a significant
element in the price of some goods, especially of raw
materials. Industries always have the possibility to
seek out alternative solutions, which will minimise
their costs, they will switch to other types of energy,
for example, or will purchase their raw materials from
closer sources.
However, it is true also
that, despite these price increases (assets, freight
rates), transportation by sea remains extraordinary
cheap and has contributed to a remarkable development
in international trade.
|
Shipping and Shipbuilding Markets in 2003
I N D E X
|