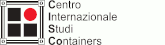
|
CENTRO ITALIANO STUDI CONTAINERS | YEAR XVI - Number 6/98 - JUNE 1998 |
Progress and technology
Il nuovo sistema di scarico/carico delle portacontainers del
Terminal Ceres di Amsterdam
Le portacontenitori di capacità pari ad 8.000 TEU ed oltre
entreranno presto in servizio commerciale sulle principali rotte
marittime, se - naturalmente - la loro utilità dal punto
di vista dell'economia potrà essere dimostrata. Uno dei
fattori-chiave per la riuscita dell'introduzione in servizio di
queste navi sarà il conseguimento di un'elevata produttività
portuale. Tuttavia, nei terminals esistenti possono essere dedicate
ad una singola nave cinque o sei gru da banchina al massimo. Se
cinque gru sono in grado di sostenere 30 movimentazioni per ora
lavorativa nel corso dell'attracco-nave, lo scarico ed il carico
dell'80% della nave richiederanno circa 53 ore lavorative e, aggiungendo
i tempi di fermo ed altre perdite di tempo, i tempi richiesti
per lo scalo presso il porto saranno dell'ordine di circa 2,5
giorni. Dato l'alto costo capitale della nave, l'armatore non
può accettare questo stato delle cose e sarà quindi
necessario un maggior tasso di produttività portuale allo
scopo di far sì che queste navi diventino entità
commerciali vitali.
La CTI (Ceres Terminals Inc) e la PMA (Amministrazione Portuale
di Amsterdam) hanno, pertanto, proposto di risolvere questo problema
mediante la messa in opera di un progetto che è sotto esame
da molti anni, vale a dire mettere la nave su uno scalo di alaggio
e lavorarla da entrambi i lati. L'obiettivo della CTI e della
PMA è quello di conseguire il considerevole livello di
produttività netta di 300 movimentazioni per ora lavorativa/nave.
La CTI in origine aveva proposto di mettere attraverso lo scalo
di alaggio grosse gru a cavalletto dotate di braccio doppio. Questa
conformazione, tuttavia, avrebbe richiesto l'introduzione di una
larga varietà di nuove tecnologie inerenti alle gru da
banchina e ciò avrebbe comportato tutti i rischi che normalmente
accompagnano un progetto di ricerca ingegneristica, unitamente
a quelli che risultano dal lavorare una nave secondo nuove modalità.
Un gruppo di programmatori formato da rappresentanti della CTI,
della PMA, della JWD, della Liftech Consultants e della Paul F.
Richardson & Associates ha, perciò, sviluppato alla
fine un piano terminalistico basato su equipaggiamenti più
tradizionali. Nel piano definitivo, vengono piazzate gru da banchina
tradizionali su normali calate su ciascun lato dello scalo di
alaggio, servite da normale equipaggiamento per operazioni terminalistiche.
Le caratteristiche principali del piano preliminare erano le seguenti:
Scalo di alaggio
Lunghezza 390 metri, larghezza 56 metri, in grado di servire navi
fino a 340 metri di lunghezza con 20 containers affiancati sul
ponte.
Banchine
- Banchina lato nord dello scalo di alaggio di 330 metri
- Banchina lato sud dello scalo di alaggio di 390 metri
- Banchina attraverso l'ormeggio di 650 metri
- Banchina feeder/chiatte di 250 metri lungo il lato nord dello
scalo di alaggio.
Piazzale contenitori
35 ettari di area di deposito netta, servita da uno dei due elevatori
a forca, con una capacità complessiva di deposito di 16.000
TEU ed una capacità produttiva di 600.000 movimentazioni/nave
all'anno.
Varco
Varco doppio con otto corsie d'accesso ed otto corsie di uscita,
in grado di servire punte di traffico pari a 1.600 contenitori
al giorno.
Piazzale ferroviario
2.240 metri di binari operativi.
Lo sviluppo di questo piano si è basato su una accurata
pianificazione, supportata da una rigorosa
simulazione computerizzata. In origine, erano state prese in considerazione
tre modalità operative:
- Elevatori a forca;
- RTG (gru a cavalletto su ruote gommate) servite da trattori
a doppio semirimorchio;
- RTG servite da trattori a semirimorchio singolo.
Ognuna di loro presentava diverse capacità produttive
e diverse punte di produttività, il cui calcolo è
stato ottenuto mediante una simulazione analitica. La Tabella
sotto riportata riassume l'equipaggiamento e le prestazioni di
ciascuna opzione.
CONFRONTO TRA I DATI OPERATIVI
|
| Elevatori a forca
| RTG con doppio semirimorchio
| RTG con singolo semirimorchio
|
Capacità produttiva (movimentazioni/anno)
| 609000 | 620000 | 695000
|
Veicoli di servizio per gru da banchina |
3-4 | 5 | 6 |
Elevatori a forca a servizio di varco e ferrovia
| 19 | - | - |
RTG a servizio del piazzale contenitori |
- | 49 | 43 |
Movimentazioni/ora presso l'ormeggio a dente
| 316 | 285 | 302
|
Movimentazioni/ora presso l'ormeggio traverso
| 111 | 94 | 100
|
Il piano che prevedeva la RTG a semirimorchio singolo ha conseguito
la più alta capacità produttiva a causa della sua
maggiore capacità di deposito in piazzale. Sia questa configurazione
che il piano basato sugli elevatori a forca hanno raggiunto l'obiettivo
della CTI, fissato in 300 movimentazioni/ora. La Paul F. Richardson
& Associates ha effettuato una esauriente analisi economica
di tutte le alternative ed è pervenuta alla conclusione
che quella inerente agli elevatori a forca presenta i minori costi
complessivi per movimentazione. Il piano che prevede gli elevatori
a forca dispone della minore capacità produttiva ma bisogna
tenere presente che la PMA ha la possibilità di ampliare
rapidamente ed a basso costo il terminal al fine di conseguire
maggiori capacità di deposito e di produttività.
Lo scalo di alaggio è stato collocato in prossimità
dell'estremità settentrionale del terminal allo scopo di
trarre vantaggio dal bacino posto all'intersezione del Noordzeekanaal
e della Amerikahaven, che costeggiano il terminal rispettivamente
in direzione nord ed est. Lo scalo di alaggio si trova in acque
protette, in assenza quindi di maree o correnti, il che agevola
la manovra di grandi navi per entrarvi od uscirvi. Il piazzale
contenitori è diviso in maniera diseguale dallo scalo di
alaggio. Molti dei contenitori manipolati presso la banchina settentrionale
dello scalo di alaggio dovranno essere messi in deposito nel piazzale
meridionale, dopo aver fatto il giro dello scalo di alaggio. Una
simulazione computerizzata ha valutato l'efficacia di questa movimentazione
e l'interazione tra stivaggio, traffico nel piazzale ed al varco
alla punta dello scalo di alaggio.
Il piano preliminare prevede nel complesso fino a dodici gru
da banchina. Di queste, quattro sono assegnate in permanenza alla
banchina nord dello scalo di alaggio, due sono assegnate stabilmente
alla banchina sud, tre possono servire sia la banchina sud dello
scalo di alaggio che la banchina convenzionale, mentre tre gru
sono assegnate stabilmente alla banchina convenzionale. Ciò
farà sì che nove gru possano servire simultaneamente
la nave nello scalo di alaggio, mentre tre di loro saranno in
grado di servire l'intera larghezza della nave a prua o a poppa
della sovrastruttura della nave.
Le sei gru assegnate in permanenza alle banchine dello scalo
di alaggio saranno dotate di bracci in grado di raggiungere tutti
i containers presso i boccaporti centrali di qualsiasi nave Panamax
o più grande. Le restanti gru saranno dotate di bracci
lunghi abbastanza da servire l'intera larghezza di navi con sino
a 20 contenitori affiancati sul ponte. Le gru al lato opposto
dello scalo di alaggio saranno configurate per lavorare sui boccaporti
laterali della nave; al fine di assicurare la sicurezza dell'operatore,
saranno necessari speciali meccanismi di guida, di controllo dell'asta
e del macchinario di sollevamento. La Liftech Consultants sta
attualmente lavorando con la McKay International, la CTI e la
PMA al fine di sviluppare le necessarie caratteristiche richieste
per le gru in questione.
(da: Cargo Systems, maggio 1998)
|